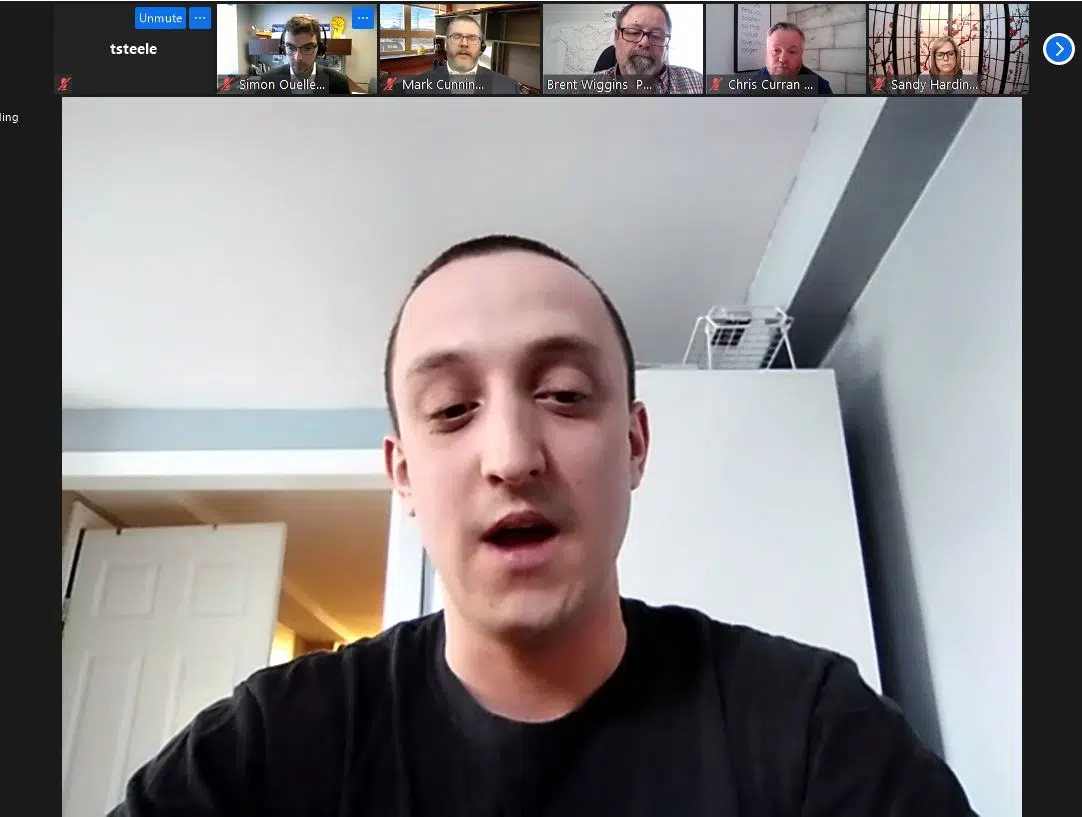
Brandon Boucher, an employee at Saint John Laundry, speaks during a CUPE media conference. (Zoom video capture)
An incident at the Saint John Laundry facility on Wednesday prompted CUPE members to call for the plant’s manager to be fired.
The facility cleans and distributes medical linen for hospitals across southern New Brunswick.
Employee Brandon Boucher, who was working on Wednesday, said when the fire alarm went off shortly after 1 p.m., staff members left the facility but were ordered back in before the fire department arrived.
“There were a couple of employees who were yelling, questioning why we were re-entering the building and we started making our way back into the building and the front hallway was all filled with water, we were walking through water because apparently, a sprinkler pipe had burst,” Boucher said.
Over a Zoom call on Friday morning, CUPE’s Mark Cunningham described the incident at the Lorneville facility.

Staff at the Saint John Laundry facility in Lornevile. (photo submitted by Service New Brunswick)
“As employees were walking back into the building they were complaining that they could smell something burning. Management at the time were brushing off the concerns [saying] ‘nothing was burning, get back to work,'” Cunningham said.
Simon Ouellette, communications representative for the Maritimes regional office of CUPE, described the situation as an example of “management putting production above human lives.”
“Rushing people in like, he couldn’t wait five minutes, 10 minutes for the fire department to come. They had to go back to their machines and get back to work cracking the whip. Who does this in 2021?” Ouellette said.
CUPE also wants two independent investigations into the March 3rd incident and into ongoing issues at the facility they say is in “constant turmoil.”
The following statement was issued on Friday afternoon by Valerie Kilfoil, spokesperson for Service New Brunswick:
On Wednesday March 3rd, 2021 at the Saint John plant the fire alarm went off. As per safety protocols, employees were evacuated at the pre-established meeting points and roll call was taken. Regular fire drills are undertaken each year at the plant as part of the safety protocols. Dedicated staff in the building completed a scan to determine source of problem. It was determined that there was a burst pipe linked to the fire suppression system and no other issues were determined. Although firefighters were not yet on site and the alarm not yet de-activated, employees were allowed back in due to the cold, windy weather since they were not dressed for the elements.
As they were returning, it was perceived that an unknown odour was apparent in a particular part of the building, although nothing visual was identified.
Employees were told to grab their coat, go to their vehicles and wait for further instructions. Firefighters arrived, completed scans and determined there no other source of issues except for the burst pipe. Employees were asked to return to work.
Total time of the incident was about 1.5 hours. Two employees were stationed through out the plant as fire watch, until burst pipe (fire suppression) was repaired. The all clear was given at 2:20 pm. Their were no injuries . As per protocol, the response to the incident will undergo a review by the Joint Occupational Health and Safety Committee and any recommendations will be actioned accordingly.